Av Jan Qvick och Göran Råberg
Då Brukskoncernens styrelse vid mötet i december 1930 beslutade att starta tillverkning av hårdmetall lämnade man öppet för koncernledningen att förlägga tillverkningen antingen i Fagersta eller i Österby. Man önskade ta fram ett nytt material som kunde konkurrera med den nya tyska hårdmetallen Widia från Krupp. Det främsta argumentet för Österby/Dannemoraverken var att de redan tillverkade snabbstål och hade därför kompetens inom skärande bearbetning. Fagersta hade dock bättre tillgång till elektrisk energi och där fanns dessutom en lämplig lokal som hade stått oanvänd sedan 1930 när ämnes borrningen till bergborrar upphört – Turbinhuset på Holmen.
Redan i januari 1931 anställdes verkmästare Gottlieb Larsson som tidigare arbetat vid Arbit i Arboga. Där hade han under flera år arbetat med att framställa detaljer i gjuten wolframkarbid, främst sandblästringsmunstycken, och man var snabbt igång med en motsvarande tillverkning i Turbinhuset. För att få fram en sintrad hårdmetall krävdes dock ett grundläggande utvecklingsarbete i synnerhet som man beslutat att inte göra intrång i några av de metodpatent som vid den här tidpunkten togs av huvudsakligen Krupp. Man ämnade heller inte begära licens på något av patenten. Förutom Larsson var det Gösta Sterky som ansvarade för utveckling och tillverkning de första åren tillsammans med den tekniske direktören Magnus Tigerschiöld. Eftersom hårdmetallavdelningen, eller Specialsmältningen som den kallades, helt saknade egna laboratorier användes brukets laboratorier och där hade även tjänstemännen sina kontor. Under hösten 1931 hade man tagit fram de första sintrade försökslegeringarna och eftersom möjligheter till bearbetningstester saknades i Fagersta utfördes dessa hos kunder och då företrädesvis kunder som redan använde Widia. En sådan var SKF i Göteborg som lade Fagerstas första order på sintrad hårdmetall i november 1931 – se Månadens Bild för november 2023.
Under 1932 fakturerade man totalt 56 kg hårdmetall och av dessa var merparten gjuten wolframkarbid. Under 1930-talet ökade kvantiteterna för varje år så att man 1939 var uppe i nära 3 ton, majoriteten sintrad hårdmetall. Redan från och med 1933 gick hårdmetalltillverkningen med rejäl vinst och under åren 1934-1939 uppgick vinsten i genomsnitt till 47% av försäljningsintäkterna för hårdmetall.
Dagens vändskär som skruvas fast i en hållare eller fräskropp av stål var inte uppfunna då, utan skären löddes fast vid verktyget. Att löda hårdmetall mot stål är inte helt enkelt bland annat eftersom materialen har väldigt olika värmeutvidgning och många kunder upplevde problem med lödningen. Detta ledde fram till att man 1935 öppnade en avdelning för verktygstillverkning och för att få plats med denna byggdes turbinhuset ut med ytterligare ett skepp mot söder. I samma veva byggdes en kontorsdel ut mot norr där tjänstemännen nu kunde få kontor. Det södra skeppet finns ännu kvar medan kontorsdelen revs våren 1988. Utbyggnaderna framgår av planritningen.
År 1933 efterträddes Gösta Sterky av Karl Bonthron som ansvarig för hårdmetalltillverkningen – en befattning som han hade till sin pensionering 1970.
Bilden visar honom i kontorsdelen till turbinhuset och vi kan sluta oss till att han hade rummet mot nordost eftersom rummet har fyra fönster varav två syns på bilden. Fagersta Bruksarkiv
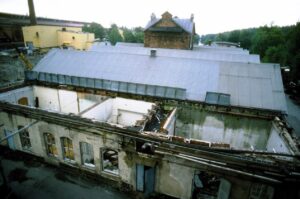
Rivning av kontorsutbyggnad mot norr på Turbinhuset 1988, Bonthrons gamla kontor var längst till vänster. Foto Göran Råberg
Krupp hade från och med januari 1931 metodpatent på våtmalning av wolframkarbid och kobolt och det tvingade Fagersta att utveckla en egen process som bestod i att man på kemisk väg fällde ut koboltkarbonat på wolframkarbidkornen. Det bildade slammet tvättades och torkades sedan med bland annat ånga. Detta processteg gjordes dock inte i turbinhuset utan i en byggnad på östra sidan av Kolbäcksån där tillgång till ånga fanns.
Sortprogrammet utökades under 1930-talet. Den ursprungliga Widia liksom Seco lämpade sig väl vid bearbetning av kortspånande material som till exempel gjutjärn medan de var mindre lämpliga vid stålbearbetning som ger långa spånor. Dessa spånor nöter en grop i skäret. Krupp hade redan 1931 kommit ut på marknaden med en sort som förutom wolframkarbid även innehöll titankarbid. Gösta Sterky hade inlett utvecklingsarbetet av en motsvarade sort från Fagersta och Karl Bonthron slutförde det så att Seco 2 kunde lanseras 1935. Ungefär samtidigt lanserades även Seco 3 som var en finkornigare och hårdare variant av den ursprungliga Seco som då benämndes Seco 1. År 1936 kom Seco 4 avsedd för träbearbetning och 1939 ytterligare en variant för stålbearbetning – Seco 5.
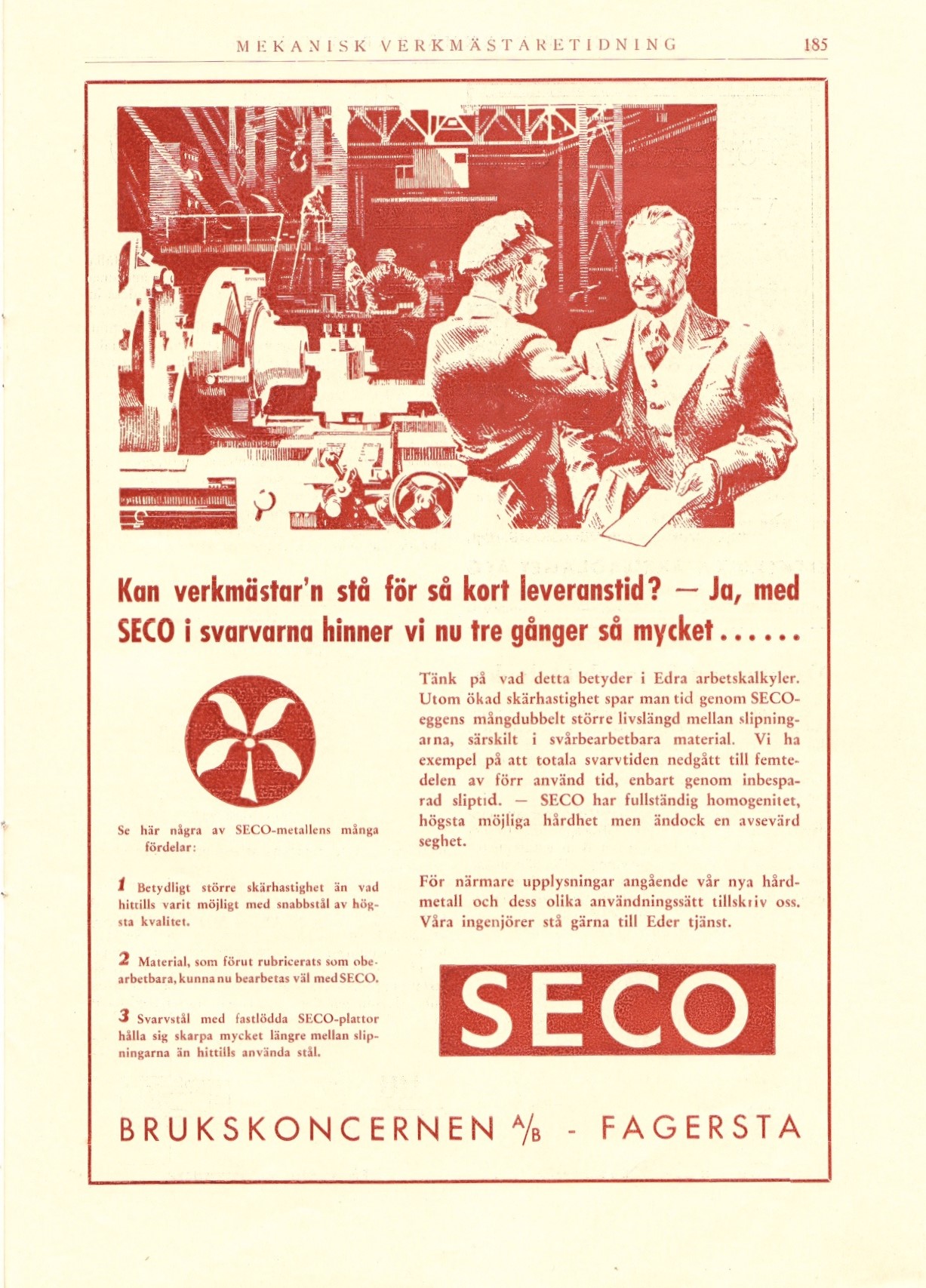
Annons från 1935 då Fagersta Bruks första sort med titankarbid, Seco 2, lanserades. Svensk Verkmästaretidning 1935
Under 1930-talet hade hårdmetall också börjat användas inom bergborrning framför allt på europeiska kontinenten i mjuka bergarter i kol- och saltgruvor. Fagerstas leveranser dit var blygsamma, men 1938 påbörjade Atlas Diesel (nuvarande Atlas Copco) försök med slagborrning i hårt berg med hårdmetallskär fastlödda på borrstål. Fagersta hakade på och började leverera hårdmetall även för bergborrning.
Krigsåren var goda år för Secotillverkningen med en årskvantitet av cirka 5 ton per år, fakturering på cirka 2,5 miljoner kronor och en årlig vinst uppgående till cirka 1,5 miljoner. Med ett allt mera differentierat produktprogram i form av flera sorter och även utökat antal geometrier på plattorna blev turbinhuset, trots tillbyggnaderna, för litet och vid årsskiftet 1941-42 beviljade Fagersta Bruks styrelse 1,4 miljoner kronor till uppförandet av en ny hårdmetallfabrik som kom att placeras norr om turbinhuset. Den dimensionerades för en årsproduktion av 30 ton och i första skedet anskaffades utrustning för 12 ton per år. Fabriken var klar för inflyttning vid nyåret 1944 varvid hela tillverkningen inklusive den kemiska koboltutfällningen flyttades dit. Turbinhuset hade dock ännu inte spelat ut sin roll inom Fagerstas pulvermetallurgiska industri. Fortsättning följer i Turbinhuset på Holmen del 3.
Några bilder från hårdmetalltillverkningen i Turbinhuset
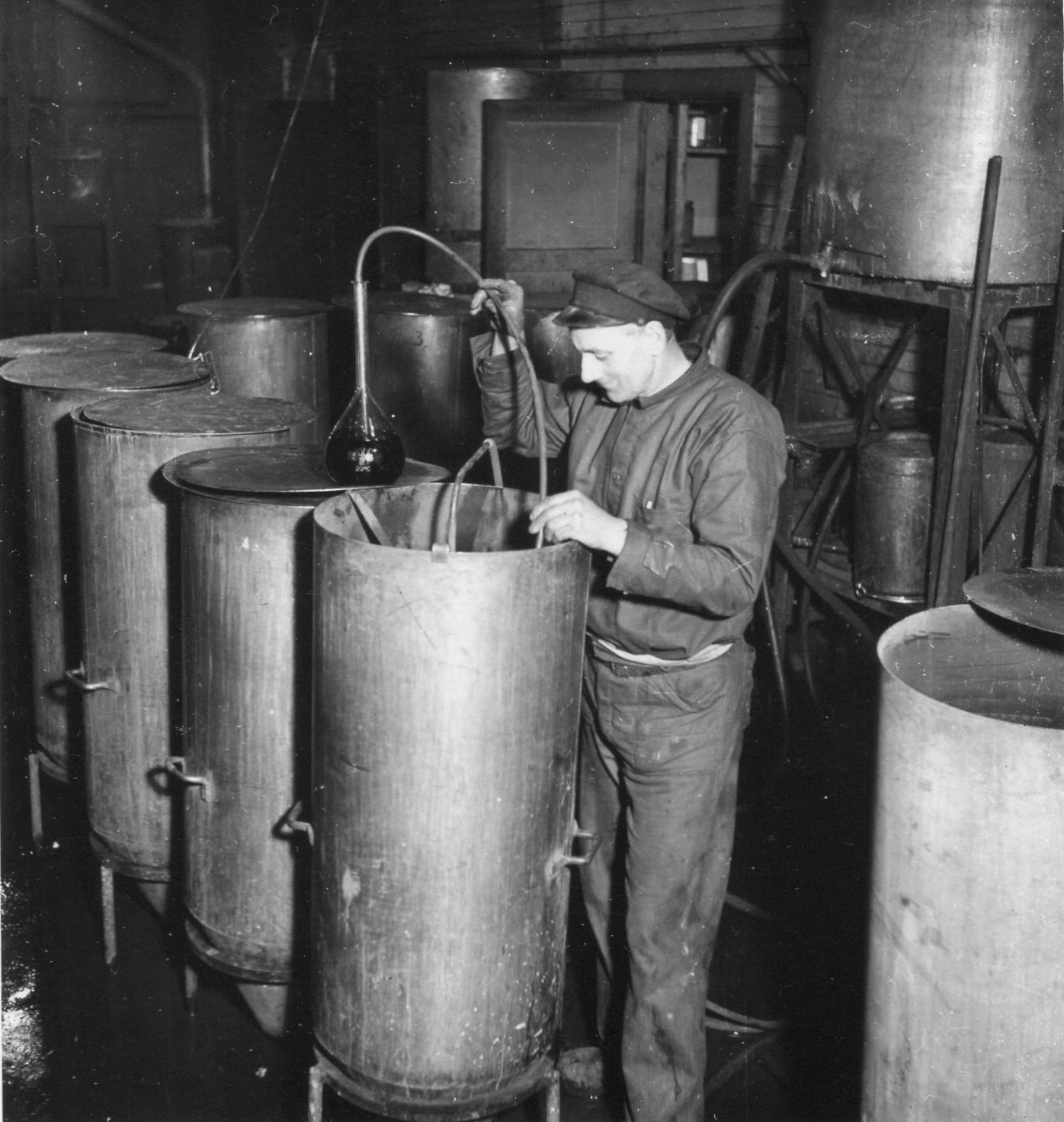
Vetterskog tillsätter under omrörning koboltkloridlösning till wolframkarbiden som är uppslammad i sodalösning. Fagersta Bruksarkiv
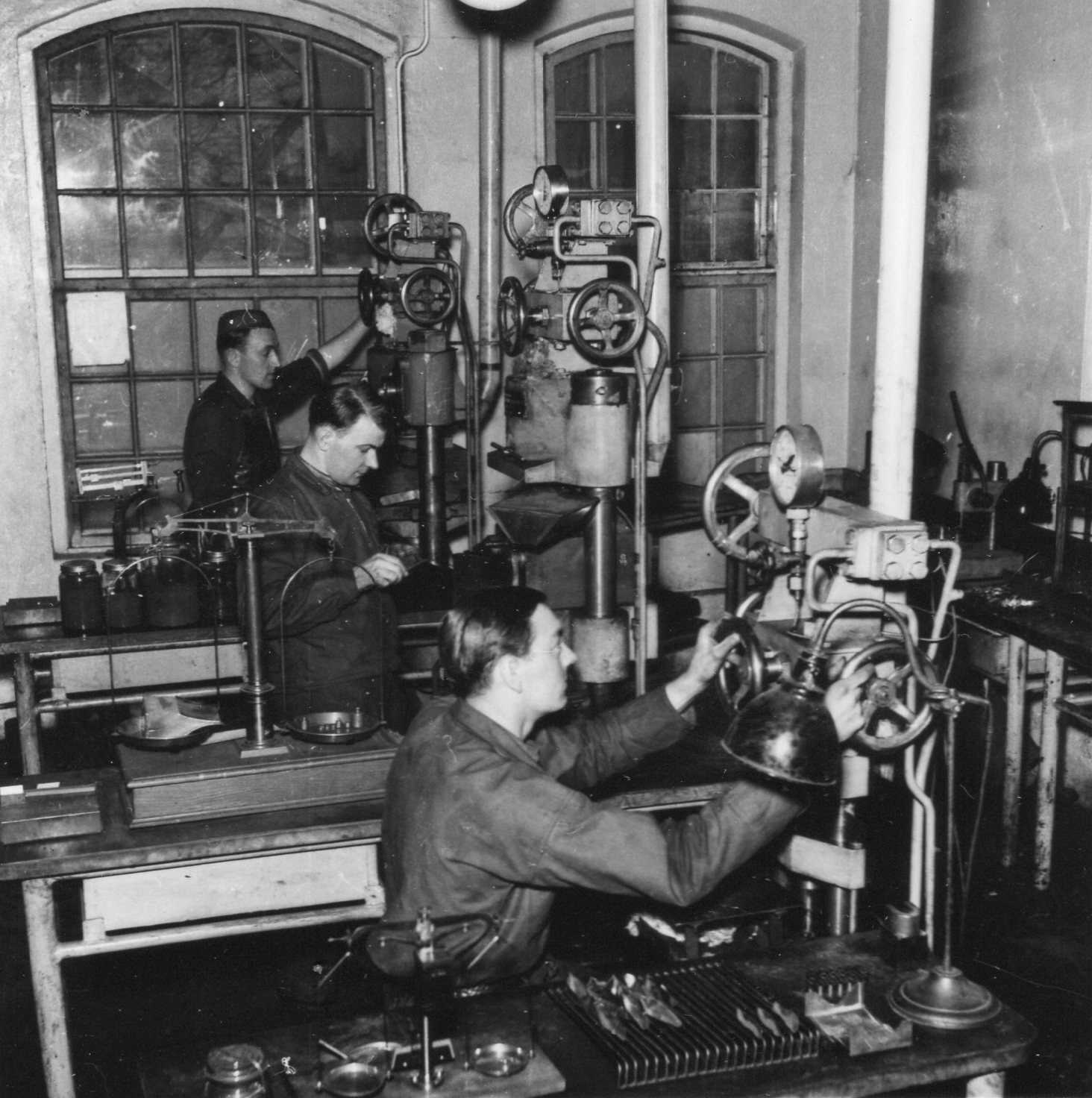
Pressar: mot fönster 80 ton, Ivar Andersson; mitten 40 ton, Otto Berggren; närmast 8 ton, Algot ? Fagersta Bruksarkiv
Källor:
Karl Bonthron, Secohistorik åren 1930-1970
Fagerstabrukens historia, del 3, Pulvermetallurgiska produkter, p 608-622